Hot Enamel in Jewelry: Art, Techniques, and Care
- pinchukwork
- Jun 7
- 7 min read
Updated: 2 days ago
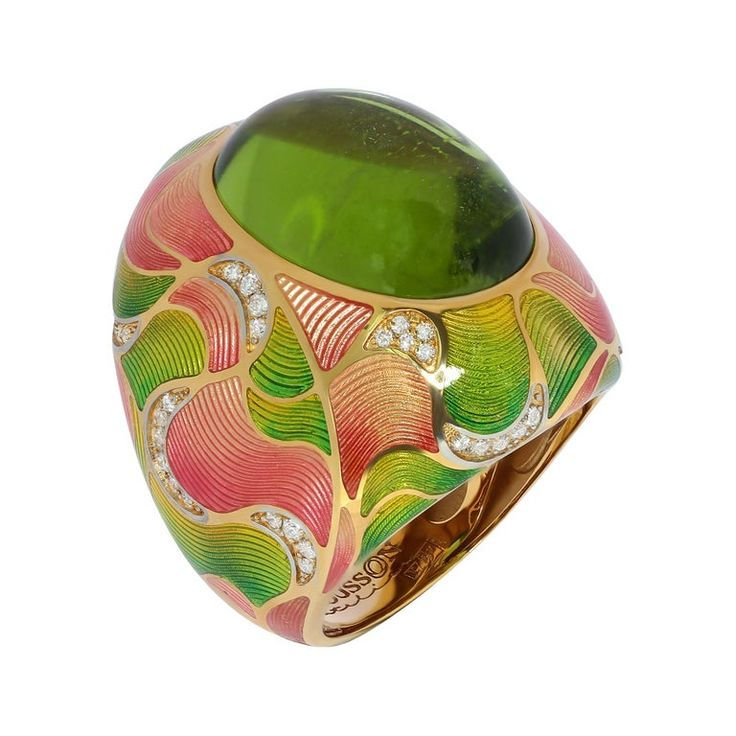
What is Hot Enamel and Why is it Unique in the Art of Jewelry?
Hot enamel is not just a technique for decorating jewelry, but a true art form that transforms metal and glass into masterpieces frozen in time. It gives jewelry incredibly bright, rich colors and a unique shine, making each piece truly spectacular and one-of-a-kind. This combination of glass and metal creates stunning color gradients and shapes, adding a special charm to any look.
The uniqueness of hot enamel lies in its ability to go beyond ordinary jewelry making, offering an aesthetic value that turns a piece of jewelry into a wearable work of art. Items created using this technique stand out in the market thanks to their distinctive, memorable aesthetics, which is a significant advantage. This attracts connoisseurs who are looking for more than just a precious item—they are looking for an embodiment of artistic thought and individuality.

The History of Hot Enamel: From Antiquity to Modernity in Jewelry Art
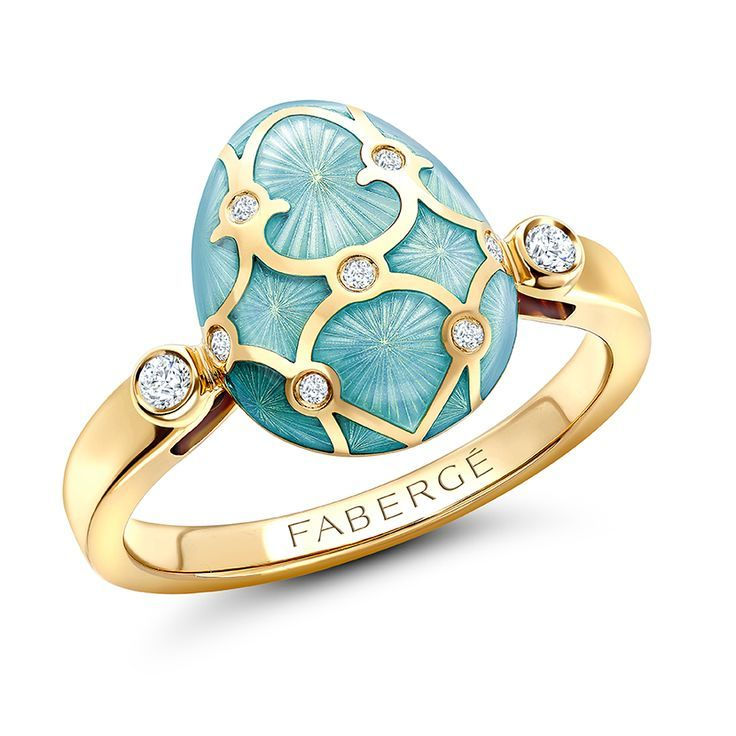
The art of enameling, much like jewelry making itself, has a history spanning over three thousand years. The exact time and place of the first fusion of molten colored glass with metal remain unknown. However, mentions of early enamel work are found in descriptions of Greek and Roman jewelry. For instance, in Mycenae (Greece), metal objects with inlaid blue glass plates dating back to 1425–1300 BC were discovered, making them some of the oldest known finds. The ancient Egyptians and Greeks would grind glass, mix it with dyes like cobalt or copper, apply it to metal, and then fuse it at high temperatures. This jewelry often carried deep spiritual meaning and was believed to provide protection.
The enameling technique reached its peak in the Byzantine Empire, where intricate enamel patterns adorned royal regalia and religious artifacts. During the Renaissance, European masters significantly refined enameling methods, making them extremely popular among nobility and aristocracy.
In the modern era, interest in hot enamel has been revived. It was popular during the Art Deco period in the 1910s, and later in the psychedelic and boho movements of the 1960s and 1970s. Today, hot enamel is one of the most significant emerging trends in jewelry art. The long and rich history of this technique, its use in creating royal and religious artifacts, and its ability to retain its beauty for centuries give it the status of not just a jewelry technique, but a true cultural heritage. This is an art form that has survived millennia and continues to be relevant. For jewelry houses specializing in hot enamel, this presents an opportunity to position their pieces as part of a great artistic tradition, not just a fashion accessory. This approach adds depth and prestige to the brand, attracting clients who value history and timeless values.
The Hot Enamel Process: How Unique Jewelry is Created

Creating jewelry with hot enamel is a complex and painstaking process that requires exceptional skill, precision, and patience from the jeweler. Each stage is performed with meticulous care to achieve a perfect result.
The process begins with preparing the material. The raw material for enamel consists of glass-like plates, which the master grinds into a fine powder. This powder is then mixed with water to form a paste. It's important to note that pure enamel itself is colorless and transparent after firing. Its bright and saturated colors are achieved by adding tiny amounts of metal oxides, such as cobalt for blue, copper for green, iron for brown, or manganese for purple.
Next is the application stage. The enamel paste is carefully applied to the surface of a gold or silver piece of jewelry. This is done with a special tool, often made or adapted by the jeweler himself to suit the specifics of his work and the complexity of the pattern.

The key stage is firing. The applied enamel is placed in a special kiln to set. The firing temperature, which can range from 600 to 900°C, and the duration (about 30 minutes) are carefully selected depending on the metal alloy and the enamel composition. Masters can fire a single piece up to 100 times, and each time, the technological procedure must be strictly followed, as the slightest deviation can ruin the piece.

After each firing, the item is cooled, and the glass film hardens, forming the enamel coating. Finally, the finishing stage begins. After all firings are complete, the piece is polished and, if necessary, returned to the kiln to achieve a perfectly smooth and shiny surface.
The extreme complexity and multi-stage nature of creating hot enamel, requiring multiple firings at high temperatures and precise control, means that each such piece is the result of exceptional craftsmanship and attention to detail, not a mass-produced product. Emphasizing this complexity and manual labor, as well as the "high quality of work," increases the perceived value of the jewelry. This attracts clients who seek exclusivity, uniqueness, and appreciate genuine art and craftsmanship in jewelry.
Types of Hot Enamel: An Overview of Jewelry Enameling Techniques
Hot enamel includes a variety of techniques, each giving a piece of jewelry its unique character and visual effect. Understanding these differences allows one to truly appreciate the craftsmanship and artistic value of the jewelry.
Cloisonné (Enamel Partition): One of the most famous techniques. Thin metal wires, often gold or silver, are soldered to a metal base, creating miniature cells or "cloisons." These cells are then filled with enamel powder of various colors and fired in a kiln. In the finished piece, the wire remains visible, creating a clear outline for each element of the design.
Champlevé (Recessed Enamel): In this technique, a metal surface (usually thicker than for cloisonné) is carved, engraved, or etched to create depressions. These depressions are then filled with enamel, while the un-engraved, raised parts of the metal remain visible, forming a frame for the enamel design.
Plique-à-jour (Stained Glass Enamel): This technique is similar to cloisonné but lacks a metal backing. The enamel is applied to cells created by metal wires, but after firing, a temporary backing is removed (e.g., with acid). This allows light to pass through the transparent or translucent enamel, creating the effect of a miniature stained-glass window, making it very complex and labor-intensive.
Painted Enamel (Limoges): In this technique, enamel is applied directly to a metal surface like a drawing, similar to watercolor or oil painting. This allows for fine details, gradients, and even photorealistic images.
Basse-taille: The metal surface is engraved or textured with a relief pattern and then coated with translucent enamel. The varying depth of the carved areas causes the enamel to take on different tones and shades, creating an interplay of light and shadow within the glass surface.
Grisaille: A monochromatic enameling process that begins with a layer of black (or very dark) enamel. White enamel is then applied over it, creating various shades of gray by varying its thickness and transparency. This creates an effect of relief and volume, simulating sculpture.

The variety of hot enamel techniques means that enamel is not a single style, but a whole palette of artistic expressions. Each technique offers unique visual and tactile sensations, allowing for the creation of pieces with deep meaning and individual character. Demonstrating a deep knowledge and mastery of these different techniques not only educates the buyer but also positions the jewelry house as an expert and leader in this niche. This can attract more sophisticated clients looking for specific, rare, or complex enamel styles.
Comparative Table of Hot Enamel Techniques
Technique | Brief Process Description | Characteristic Visual Effect | Level of Difficulty |
Cloisonné | Thin metal wires are soldered to a base, creating cells that are filled with enamel and fired. The wire remains visible. | Clear, color-separated patterns with visible metal outlines. | High |
Champlevé | A metal surface is carved or engraved to create depressions that are filled with enamel. The un-engraved parts remain raised. | Enamel lies in recesses framed by raised metal outlines. | High |
Plique-à-jour | Enamel is applied into cells without a backing, allowing light to pass through. | A miniature stained-glass effect, transparency, and play of light. | Very High |
Painted Enamel | Enamel is applied directly to a metal surface in the manner of a painting. | Fine details, gradients, and photorealistic images. | High |
Basse-taille | Metal is engraved or textured before applying translucent enamel. | Play of light and shadow, depth, and volume from the relief under the enamel. | High |
Grisaille | Monochromatic enamel (often white on a black base) to create shades of gray and simulate relief. | A sculptural, three-dimensional effect in shades of gray. | High |
Benefits of Hot Enamel Jewelry: Durability and Uniqueness

Jewelry with hot enamel is not just a beautiful accessory but also a valuable acquisition that can become a family heirloom. Its durability and unique properties make it a wise investment in beauty and legacy.
Hot enamel is exceptionally strong and wear-resistant. It is resistant to high temperatures and corrosion and is extremely difficult to scratch. Unlike cold enamel, hot enamel does not tarnish and fades very slowly, retaining its original appearance for decades. This is achieved through carefully crafted partitions, uniform filling of the material, and a special shine. Furthermore, adding nano-ceramics to the enamel composition makes it even harder and more wear-resistant, providing additional protection and longevity to the piece.
Such jewelry possesses incredible durability, allowing it to be passed down from generation to generation while preserving its beauty and value. This ability to maintain its pristine look for decades directly impacts its value as an "investment in beauty" and a potential family heirloom.
In addition to its practical benefits, each enameled piece has a unique design. Thanks to the complexity and diversity of the techniques, hot enamel jewelry looks bright and one-of-a-kind, becoming an exquisite addition to any look. Positioning hot enamel as a long-term investment, rather than just a purchase, enhances its appeal to customers seeking something eternal and meaningful. This also highlights the quality and reliability of the product, which is a crucial factor of trust in the luxury segment.
Caring for Hot Enamel Jewelry: How to Preserve its Shine for Years

To keep your hot enamel jewelry beautiful and shiny for years to come, you need to follow a few simple but important care rules.
First, proper storage. Enameled items should be stored in a cool, dry place, away from direct sunlight. Excessive heat or prolonged sun exposure can cause the enamel to fade or change color. It is recommended to use special jewelry boxes or soft pouches to prevent scratches.
Second, gentle cleaning. To clean enameled jewelry, use warm water, a small amount of mild liquid soap, and a very soft cloth. Gently wipe the surface, then rinse with clean water and dry. It is crucial to avoid abrasive materials and harsh chemicals such as perfumes, detergents, or chlorine, as they can damage the delicate enamel surface.
Providing detailed care instructions for enameled items shows concern for customers and their purchases. This is not just a sale, but the building of a long-term relationship. This approach increases trust in the brand and underscores its expertise not only in creating but also in preserving the value of jewelry. This encourages repeat purchases and recommendations, as customers feel supported and confident in their choice.